Just another WordPress site - Ruhr-Universität Bochum
Micromechanical and Macroscopic Modelling
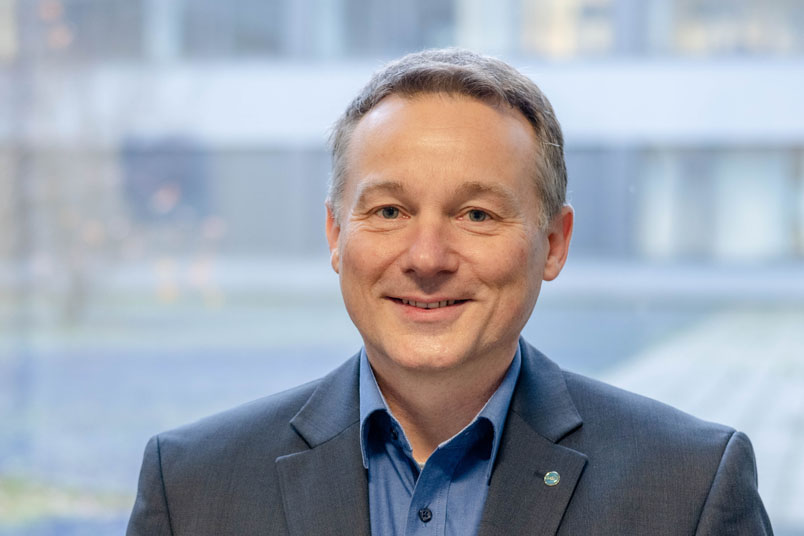
Professor
Room: 02-517
Tel.: +49 234 32 29314
E-Mail: alexander.hartmaier@rub.de
Research
We derive such microstructure-property-relationships to predict macroscopic mechanical properties of materials like strength, hardness, and fracture toughness by employing the methods of computational materials science and multiscale modelling. To accomplish this, we typically start from macroscopic models that describe an engineering application or laboratory experiment and introduce information about mechanisms or material parameters derived from more fundamental scales; see Figure 1 for an example about scalebridging in fracture modelling.
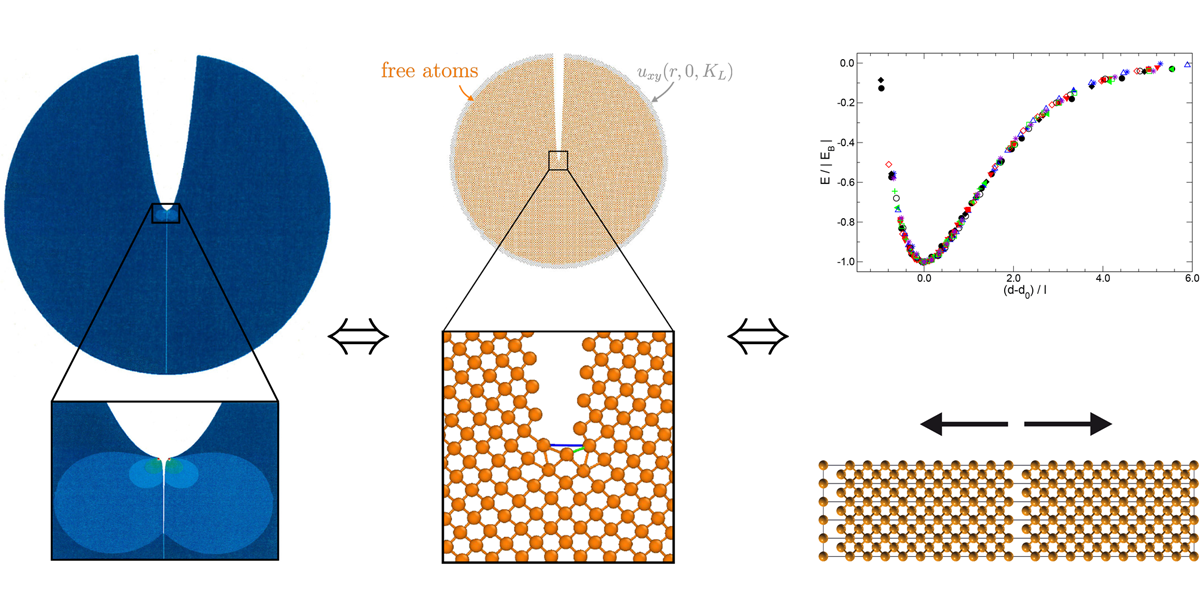
Macromodels typically do not consider the microstructure of a material explicitly, but are based on the idea of homogeneous material behaviour, which is a severe restriction of such models. However, they can be very useful to identify critical regions with high mechanical stresses and strains within potentially damaging component or loading conditions. At such critical spots, a micromechanical model is employed that explicitly takes into account the local microstructure and mechanical conditions taken from the macro-simulation and is applied as boundary conditions to the microstructure model. The microstructure in such micromechanical models is described by representative volume elements (RVE) that can be developed on different purpose-specific levels of detail, to represent either phases as homogeneous regions or individual grains within phases or even sub-structures within grains. Such micromechanical models serve mainly two purposes: Firstly, they yield insight into the critical deformation and failure mechanisms and how they depend on the microstructure and local thermal, mechanical and chemical conditions of the material. Secondly, they provide the basis for macroscopic descriptions of material properties in the form of flow rules as they are used in continuum plasticity. This latter step of developing macroscopic flow rules based on micromechanical models is termed homogenisation and can be used to take microstructural properties and mechanisms implicitly into account in macroscopic models of engineering problems.
Groups
The groups of the department are:
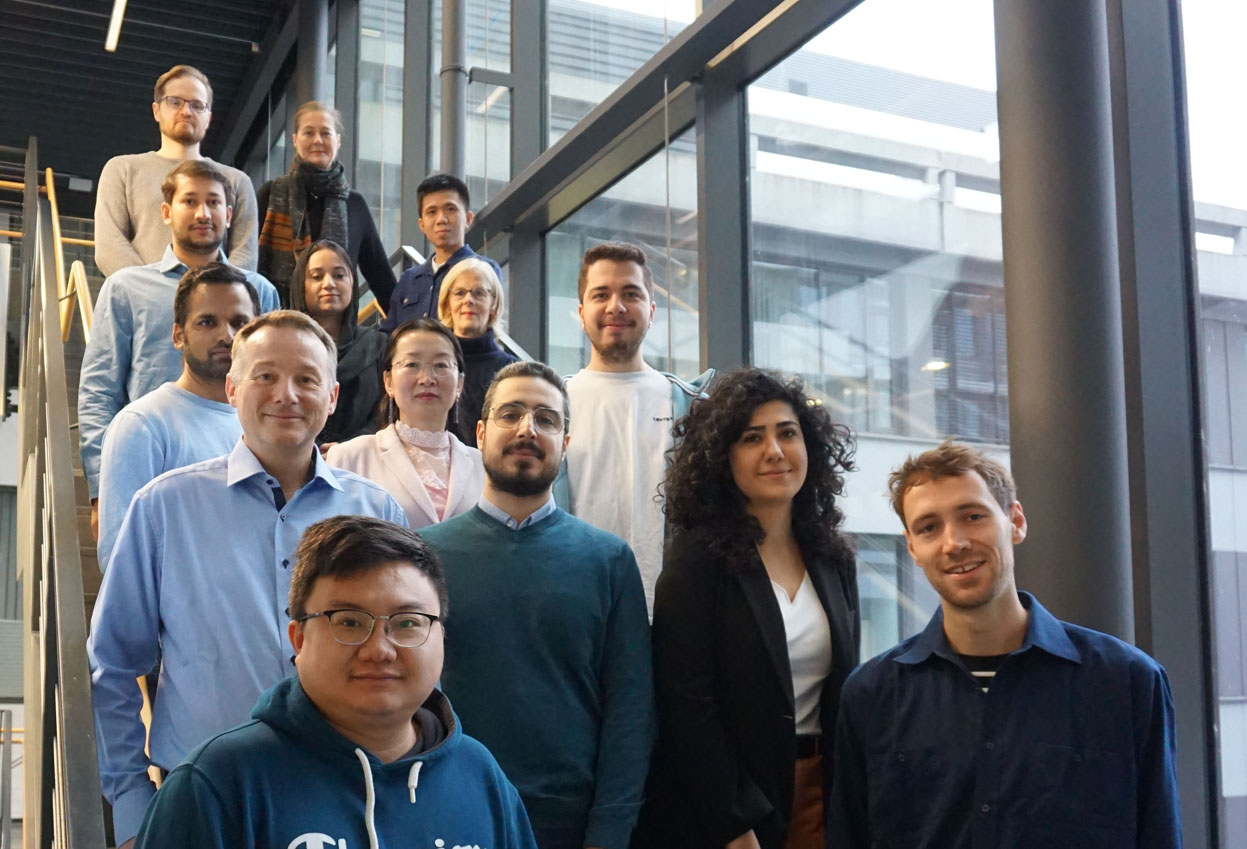
Department of Micromechanical and Macroscopic Modelling
ICAMS
Ruhr-Universität Bochum
Universitätsstr. 150
44801 Bochum
Germany
Building/Room: IC 02-515
E-Mail: mmm-office@icams.rub.de
Tel.: +49 234 32 29368
Office hours:
Mon – Fri: 10.00 a.m. – 12.00
and 1.00 p.m. – 3.00 p.m.